What’s one of the easiest, most cost-effective ways to maintain your hydraulic equipment? If you grease to spec and stay consistent with maintaining your hydraulic equipment, you can possibly eliminate unnecessary repairs, increased operating costs, prolonged downtime and you might even increase the life expectancy of your hydraulic equipment...and who doesn't want that right?
So simple, yet so effective and cheaper than any premature failure!
As with any good proactive hydraulic maintenance plan, you should also be checking your maintenance records to make sure that they are accurate. You may also need to implement a detailed lubrication routine as part of your preventative maintenance plan if you want to achieve long-term success with your hydraulic equipment.
While greasing your hydraulic equipment to spec may be one of the easiest methods of proactive maintenance, it is also one of the most overlooked ways for providing a long and happy life for your hydraulic systems and/or components. Here are a few tips to consider when outlining a hydraulic maintenance plan for lubricating your equipment...
For BEST RESULTS, you should consider managing your machines’ reliability by sticking to this simple to follow plan by using the "6 RIGHTS" for adding lubrication to your maintenance plan...
- Use the RIGHT LUBRICATION
- In the RIGHT PLACE
- At the RIGHT TIME
- In the RIGHT QUANTITY
- In the RIGHT WAY
- Under the RIGHT CONDITIONS
Have You Considered Instituting an Identification Chart?
Creating consistency with symbols and/or colors that follows a specific plan for what is needed for your equipment to be serviced properly can be crucial. You should consider incorporating this process (or one like it) into all of your training programs and maintenance plans. It should also be stressed to ALL your employees that this process is a MUST FOLLOW PLAN for properly maintaining your hydraulic equipment. If this plan is followed correctly, you should have piece of mind knowing that your hydraulic equipment is being properly lubed and well maintained.
How easy should it be to follow a lubrication identification chart?
Well, unless your employees are color blind or failed kindergarten, they should be able to choose the right grease every time. However, if any of your employees are possibly color blind, then to accommodate these team members in the workplace, you should consider substituting color for symbols or maybe use the symbols in conjunction with a color chart...either way, the goal is to make it simple to follow!
Is all this labeling and charting worth the hassle? ABSOLUTELY! Below is an example of a chart that could be used in the workplace to help your employees recognize what is needed to lubricate your hydraulic equipment properly every time. Feel free to "borrow" if needed...
EXAMPLE OF AN IDENTIFICATION CHART:
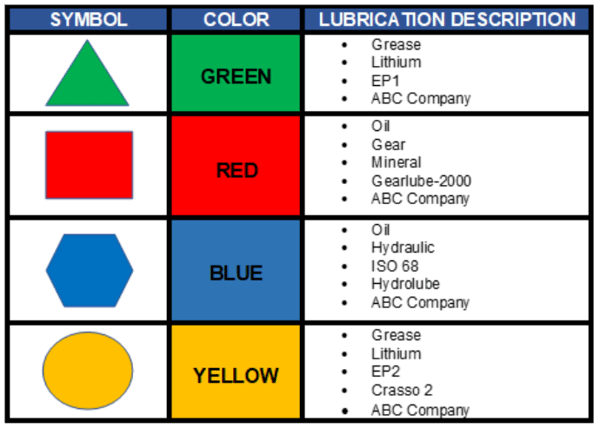
As you know, your process is only as good as the tools you have to use!
Grease Guns are an essential tool for lubricating your hydraulic equipment. Most grease guns have many great attachments that allow you to get into those hard to reach areas with a little less frustration. If you install a meter on your grease gun, you will be able to measure how much grease is being used by your team. If you choose to keep track of how much grease is being dispensed, you can then log the usage in your maintenance records for use in future repairs and/or PMs.
Pro Tip: remember to log all your data and meter readings for optimum results!
What's another best practice to consider for eliminating guesswork for your maintenance staff? You should consider marking lubrication points on the machinery with labels. When used properly, the labels should identify the proper amount (and frequency) of lubrication required for that specific machine. Maybe you should consider color coding labels to correspond to the appropriate grease gun? Just a thought...
HERE ARE SOME HELPFUL TOOLS TO HAVE ON HAND:
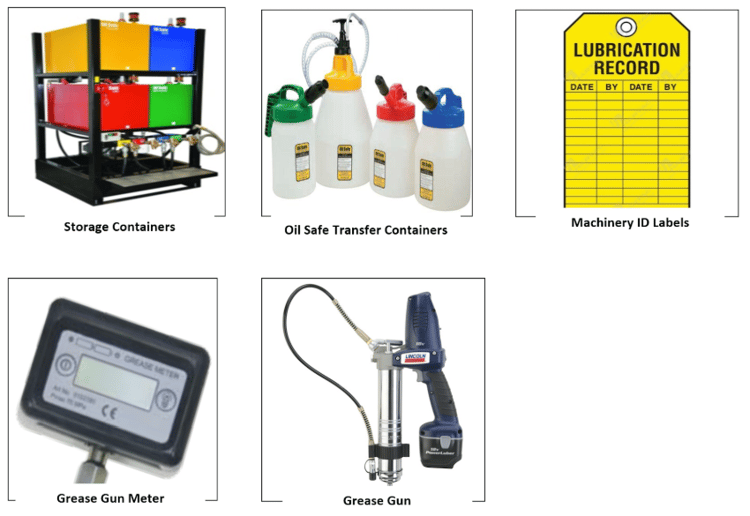
On the flip side, something to avoid is boundary lubrication...
Boundary Lubrication occurs when metal-to-metal contact between two sliding surfaces of the machinery exists. This typically occurs under high-load and low speed in piston rings, bearings, pumps, gears, etc… Why does this happen? It often occurs because the hydrodynamic film begins to thin due to speed, load and/or viscosity. Why could this be a potential problem?
The heat generated by this occurrence will eventually cause bearing failure! But don't take my word for it...ask a tribologist! Yes, there is an actual science called tribology.
Tribology is the Study of Interacting Surfaces in Motion. This science is the science of wear, friction, and lubrication and how interacting surfaces behave in relative motion in natural and artificial systems. This includes lubrication...
Tribologists suggest that as much as 70% of wear occurs during the start-up and shutdown phases of machinery. To learn more about tribology, go to https://www.ggbearings.com/en/company/tribology.
But don't worry, you can successfully reduce boundary lubrication with the right viscosity level!
Viscosity is the single most important physical property of a fluid. For this to help you in properly maintaining your hydraulic equipment, it might help you to first understand the basics of viscosity. Simply put, it’s the measure of the fluid’s resistance to flow. For example, water has a LOW viscosity of 1cSt, while honey has a very high viscosity of about 1,000 cSt. If you don’t pay attention to viscosity indexes when selecting a lubricant, your machinery’s internal sliding parts may not be adequately lubricated. If this happens, you run the risk of maximizing the threat of dangerous friction affecting the performance of your hydraulic equipment. So what actually happens if viscosity level become too low or too high?
TOO LOW - metal surfaces can’t keep separated, metal-to-metal contact occurs
TOO HIGH:- increases in oil’s molecular friction, layers of oil slide past each other, increasing operational temperatures and energy loss - this results in slower flow and thicker fluid (not good)
It's also a good practice to consider the environment, temperature and speed of the machine when determining your viscosity levels. As temperature and speed increases, the viscosity of a lubricant will decrease. Each machine should be formulated with what provides the most sufficient layer of lubrication to reduce friction. For example, a higher base oil lubricant can increase reliability with high-load capabilities.
Choose the right grease for the right conditions. So many questions need to be considered (temperature, speed, load, moisture and vibration) before selecting the appropriate lubrication and it can seem overwhelming. However, your maintenance plan has all the answers you need.
HERE'S A CASE STUDY YOU MIGHT FIND INTERESTING:
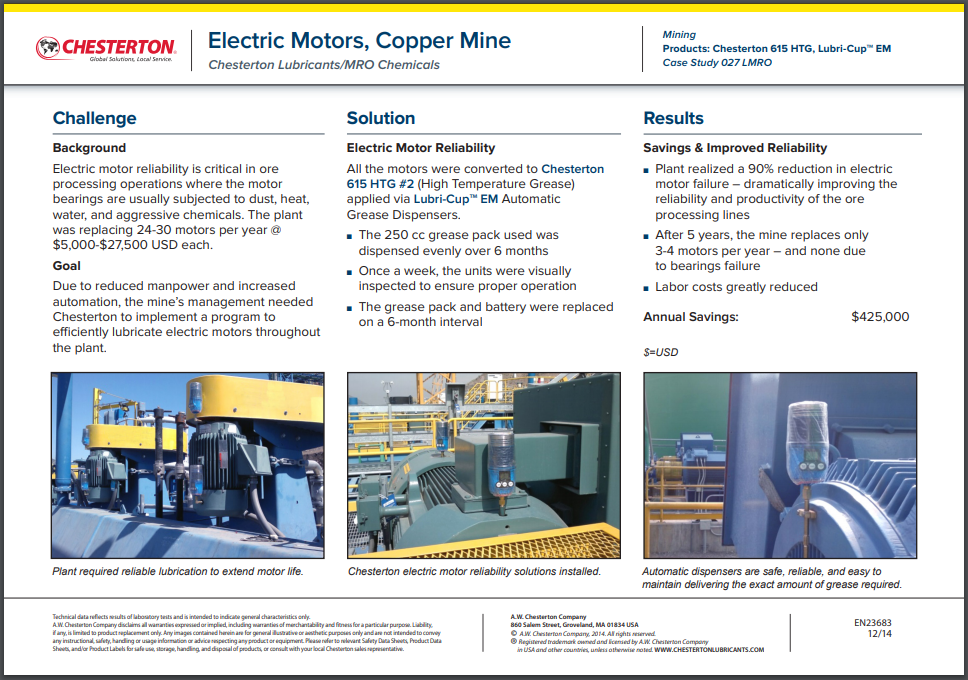
At one mine location, a lubrication survey uncovered several motor bearing failures. The motors were subjected to dust, heat, water, and aggressive chemicals. The plant was replacing 24-30 motors per year, at a cost of between $5,000 and $20,000 each. The survey resulted in a recommendation to use a higher performing grease. Following the change, the plant realized a 90% reduction in motor failure—drastically improving the reliability and productivity of the processing lines. After five years of sticking to their new lubrication plan, the mine’s maintenance staff replaces only 3-4 motors per year—and none were due to bearing failure. To learn more about this case study, go to https://bit.ly/2VSuDLQ.
Are you looking for additional help with outlining a lubrication plan? Consider downloading a copy of our popular eBook "10 Steps to Prevent Hydraulic Downtime" below...you'll be glad you did!
Download Your Copy of our 10 Steps to Prevent Hydraulic Downtime eBook Here...
![]() |
If you have additional questions about properly lubricating your hydraulic equipment, please pick up the phone and give us a call at 856-241-1145, we can help you!